Le J.B. Project... Par Spoutnik et M.O.I.
Comme promis voici le petit reportage sur la création par M.O.I. et moi de notre aile volante, la JB. On a appelé ça le JB PROJECT. Pour couper court aux questions quant au nom « JB » c’est venu après une séance de « Bill & John » et donc pour éviter un quelconque plagia on a décidé d’inverser les lettres. Et donc non ce n’était pas par rapport à la marque de whisky (on n’est pas que des alcoolos tout de même !). Le plan est « maison ». La forme ressemble un peu à celle du Su-27 FLANKER auquel on aurait coupé le fuselage au niveau du bord de fuite des ailes, avancé les 2 dérives.
Le schéma montre grossièrement la forme générale de l’appareil.
Et oui les soirées de permanences permettent souvent de laisser libre cours à l’imagination mais arrivé à presque minuit et après quelques binouzes pour aider à se concentrer, il faut aller se coucher. Comme dirait l’adage, la nuit porte conseille. Effectivement ce fut le cas. Pour arriver à nos fins, un budget de 180€, appareil en ordre de vol, a été jugé acceptable sachant qu’il s’agirait d’un prototype. On a également cherché à obtenir un appareil conciliant légèreté et résistance : pas le choix, on fibre de l’EPP !
Voici les ingrédients de la recette pour le fuselage : - Bloc d’EPP de 90mm d’épaisseur - Résine - Fibre de verre sergé en 48g - Fibre de verre sergé en 150g - Fibre de carbone - Dépron de 6mm - Une baguette de contre-plaqué de 2mm
1 – Traçage et découpe des différentes parties :
Le traçage a été effectué sur le bloc d’EPP. Dans l’optique de faire un modèle « en spare » cette opération a été réalisée 2 fois.
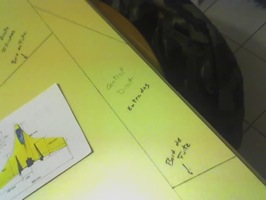 | 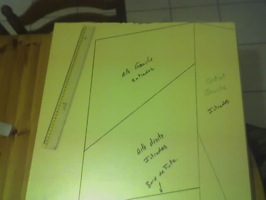 |
Pour la découpe, on passe au fil chaud. (l’installation est rustique mais elle fonctionne). Après quelques petites suées (faut pas se rater), on obtient la forme générale de l’appareil.
2 – Découpe du profil :
Le profil d’aile choisi est un profil d’aile volante : auto-stable à vitesse élevée (merci JC). Tout comme précédemment, la découpe a été faite au fil chaud. On obtient après un petit ponçage des très jolies formes.On en profite juste après pour poser la clef d’aile...
3 – La « peau de bêêête » :Le tissu utilisé est en 48g pour toute l’aile avec une bande en 150g pour le centre de la partie ventrale car c’est elle qui prend lors de l’atterrissage. Du tissu d’arrachage a été posé pour faire office de charnière. Histoire de rigidifier le tout quelques mèches de carbone ont été disposées sur l’aile (intrados et extrados).Pour ne pas perdre de temps, les dérives en dépron ont également été fibrées et rigidifiées (pour éviter le flutage). Le pylône qui va supporter la turbine a un cœur de dépron fibré au carbone (comme ça pas de soucis de résistance). On a utilisé une pompe à vide pour avoir le meilleur résultat possible.
4 – La turbine :Pour propulser la bête, on s’est dirigé vers une turbine électrique de 74mm de diamètre. Cette dernière était livrée avec un moteur brushless de 2450kv. D’après le constructeur, elle est sensée développer 1150g de poussée sous 13,5v. Après conseils d’un ancien motoriste réacteur sur Mirage 2000, la forme de la tuyère a été créée (encore une fois merci JC pour le coup de mains) en polystyrène découpé à la cnc. Comme pour le reste de la cellule, on a fibré et ajouté une mèche de carbone en sortie de tuyère pour la rigidifier. Vous pouvez remarquer que c’est vraiment de l’artisanal !!!
Mais après « démoulage » la forme est propre. La preuve...
5 – Sortie du sac et pose de la turbine et des dérives :La sortie du sac après quelques temps sous vide s’est fait sans soucis. On a tout de même dû poncer les différentes pièces pour avoir un état de surface plus acceptable (oui on a eu la main un peu lourde sur la résine). Après assemblage des dérives sur le fuselage, pose du pylône carbone et centrage de la turbine sur ce dernier, on a pu contempler le résultat de ce petit moment de délire d’un soir de permanence.
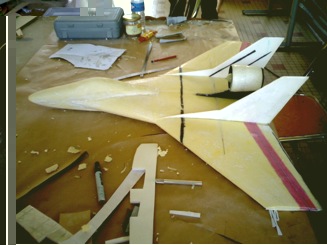 | 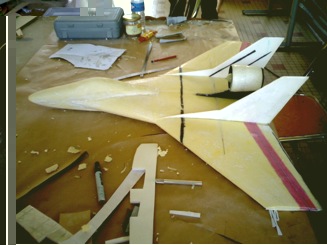 | La fin approche mais il faut poser l’électronique...
6 – L’électronique :
Voici les composants utilisés : - Contrôleur 40A avec BEC - Accu LiPo 2100mAh en 15C - 2 servos 9g de 1,2kg/cm - Récepteur 5 voies - 2 rallonges pour servos Bon j’avoue que le travail d’évidage a été fait à la barbare. Pas trop le choix car on est limité en équipement. Par contre pour éviter que les composants prennent un coup de chaud, on a dû faire des ouïes pour refroidir tout ça. Le contrôleur a été placé près de la turbine, les servos proches des flaperons et le récepteur ainsi que l’accu dans le « pif » pour avoir un centrage le plus correct possible.
La JB est née ! Elle pèse 1Kg tout rond à la naissance mais en ordre de vol.
7 – Le vol d’essai :
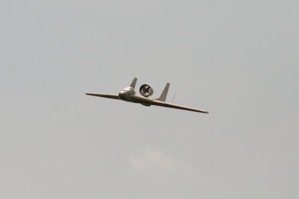 | | Par contre une fois sur le terrain, on s’est aperçu d’une chose: Comment lancer l’engin ? Et oui des fois on oublie certains éléments « pratiques ». Je m’y colle pour le lancer (lance aussi fort que t’es bête ! dirait MOI). Après quelques déboires, l’engin prend l’air. |
La turbine ronronne en vol à cause d’une résonnance entre la turbine et son pylône (uniquement pour une plage de régime moteur). L’engin est très très joueur sur le roulis par contre un peu poussif sur les montées au goût de pilote. MOI s’est senti plus serein une fois la bestiole posée. Il en avait les mains toutes tremblantes
Résultat des courses, on a une aile volante joueuse mais plus lente que prévue mais aussi plus lourde de 200g. Par contre le budget a été respecté car on s’en tire pour à peine 160€. 8 – La renaissance :
Après quelques temps passée au « placard », je décide de changer la motorisation pour qu’elle soit plus vive et plus facilement lançable. Après quelques recherches sur le net, je trouve une motorisation qui semble prometteuse. Un « petit » brushless de 5100kv (contre 2450 avant). Histoire d’assurer le coup j’en profite également pour changer l’accu, je passe d’un 2100mAh en 15C à un 2200mAh en 25C. Par contre le moteur étant plus long mais plus fin que le précédent (qui n’était en fait qu’encastré), je l’ai calé avec de la durite ce qui permettra en plus d’absorber une partie des vibrations. Je l’ai tout de même vissé sur le logement pour éviter les mauvaises surprises. Reste plus qu’à bien positionner le rotor sur l’arbre moteur.
J’avoue que j’ai fait un test tout de même avant de bien tout caler… La turbine hurle comme pas possible. Vivement le vol !
9 - Déboires :
Ben il fallait s’en douter à force d’hurler la turbine m’a lâché. Je m’explique. Samedi aprem je passe en coup de vent au terrain pour essayer de faire un petit vol de « qualification ». Je mets les gazs pour vérifer et là… PAF ! Une des pales a cassé et le rotor en a profité pour faire un bon de 10m… Et j’étais à peine à 50%... Va donc falloir refaire un rotor entier. Je vais essayer de le faire en carbone histoire qu’il n’y ai plus ce genre de mésaventure...
|